Batteries électriques : l’Europe sonne la charge
Maîtriser la filière des batteries électriques devient essentiel pour la survie de l’industrie automobile européenne. Mais l’Union rencontre des difficultés pour mobiliser les énergies et, surtout, coordonner les initiatives.
Sur un vaste espace de terre gris ocre, grand comme 60 terrains de football, les tractopelles et niveleuses s’activent. Rien ne s’élève encore dans la bourgade de Skelleftea, en Laponie suédoise, mis à part les grands résineux de la forêt boréale qui bordent le chantier. Ici, dans moins de cinq ans, devrait se dresser une immense usine de production de batteries appartenant au consortium européen Northvolt. La « gigafactory » scandinave, capable de cracher ses 32 gigawattheures (GWh) par an de capacité de stockage, rivalisera avec l’usine de Tesla dans le Nevada, à ce jour la plus grande au monde.
Ce site perdu aux confins de l’Europe est l’un des théâtres d’opérations de la grande bataille des batteries qui arrive. Un vaste affrontement économique en gestation, à l’échelle des continents, qui pourrait avoir autant de conséquences au XXIe siècle que la course à l’approvisionnement pétrolier en a eu au milieu du XXe.
Derrière cette lutte de titans, se profile la question de l’avenir de l’automobile. Le futur de la mobilité sera électrique, c’est désormais une quasi-certitude. En Europe, en Asie et, dans une moindre mesure, en Amérique du Nord, l’urgence climatique et, par effet domino, les pressions de l’opinion et des gouvernants à travers de nouvelles régulations conduisent à un remplacement du moteur à combustion par le moteur électrique alimenté par une batterie.
40 % du prix final d’une voiture
Dans l’Union européenne (UE) par exemple, l’industrie automobile est sommée, sous peine d’amendes pouvant s’élever à des centaines de millions d’euros, de réduire ses émissions de CO2 de 37,5 % entre 2021 et 2030 et ipso facto de basculer sa production de voitures neuves vers l’électrique.
Selon une étude du Boston Consulting Group, en 2017, 5 % des véhicules vendus dans le monde étaient équipés d’une batterie pour la propulsion, qu’ils soient hybrides ou 100 % électriques. En 2025, ce ratio pourrait monter à 25 %, puis à 50 % en 2030. Et le phénomène aurait même tendance à accélérer : le géant japonais Toyota a annoncé début juin que la moitié de sa gamme serait constituée de véhicules électrifiés, hybrides compris, en 2025, contre 2030 visé initialement.
Conséquence : pour la seule Europe, les besoins en cellules de batteries pourraient atteindre 400 GWh par an à l’horizon 2025, autrement dit, l’équivalent de plus de dix gigafactorys. Or, dans une voiture totalement électrique, la batterie représente 40 % du prix final, d’après une évaluation communément admise dans l’industrie. Et, selon une étude récente du centre énergie de l’Institut français des relations internationales (IFRI), l’électrochimie des cellules représente 70 % de la valeur totale d’une batterie. Conclusion : celui qui maîtrise la chimie de la batterie détient un maillon majeur de la future chaîne de valeur de l’automobile.
« Il est évident qu’être entre les mains de deux ou trois fournisseurs asiatiques entraîne une grande vulnérabilité », affirme Yann Vincent, directeur industriel de PSA
Il fut un temps, plutôt lointain, où l’avance technique et l’innovation en matière d’électrochimie étaient européennes. « C’est un Français, Gaston Planté, qui invente en 1859 le premier accumulateur, c’est-à-dire une batterie [au plomb] rechargeable », rappelle Alain Beltran, chercheur en histoire de l’électricité à la Sorbonne.
En 2019, la situation est tout autre. La production industrielle des cellules de batteries pour véhicules électriques, aujourd’hui à base de technologie lithium-ion, est dans les mains des constructeurs coréens, chinois et japonais. Le continent asiatique concentre 89 % de la capacité produite en 2018. Et les grosses usines hors d’Asie appartiennent aux coréens LG Chem, SK Innovation ou au japonais Panasonic.
« Nos approvisionnements en batteries sont sécurisés jusqu’en 2021, explique Yann Vincent, directeur industriel de PSA. Mais il est évident qu’être entre les mains de deux ou trois fournisseurs asiatiques entraîne une grande vulnérabilité. » Un danger pour la souveraineté souligné par l’IFRI : « Cette situation est particulièrement risquée ; en cas de défaut d’approvisionnement en cellules de haute performance, l’industrie automobile européenne pourrait perdre la bataille du véhicule électrique. »
Déjà aujourd’hui, des signes de pénurie existent. « Actuellement, mon problème, ce n’est pas tellement de vendre des voitures électriques,explique Lionel French Keogh, le directeur général pour la France de Hyundai, le constructeur coréen qui propose la gamme de véhicules électriques la plus complète du marché. Le souci du moment, c’est l’approvisionnement en batteries, qui est en train d’allonger les délais de livraison de nos modèles. »
Le réveil européen
Le sujet ne quitte plus l’actualité. Volkswagen va injecter 900 millions d’euros dans le projet Northvolt. De son côté, le gouvernement français avait posé comme condition de son acceptation de la fusion Renault-Fiat-Chrysler une participation à un futur « Airbus des batteries ».
A l’échelon politique comme industriel, chacun prend conscience de l’urgence de la situation et un homme, le Slovaque Maros Sefcovic, commissaire européen à l’énergie, est en train de fédérer les énergies. « Pour l’Europe, le marché des batteries, c’est 250 milliards d’euros dès 2025 et un potentiel de 2 à 3 millions d’emplois, explique-t-il. Nous allons être plus dynamiques dans les batteries que nous ne l’avons été dans la microélectronique par le passé. Nous devons nous inspirer du succès d’Airbus, exemple de coopération industrielle, mais aussi financière, politique, institutionnelle, diplomatique… »
Le résultat est la création d’une Alliance européenne de la batterie à laquelle ont adhéré 260 entreprises, avec un potentiel d’investissement mobilisable de 100 milliards d’euros. Deux projets émergent déjà. D’une part, le consortium rassemblé autour du suédois Northvolt, créé par des anciens de Tesla, a pour but de maîtriser l’ensemble de la chaîne de production des batteries, des matières premières à la fabrication, jusqu’au recyclage. Il a levé, mi-juin, 1 milliard d’euros auprès de Volkswagen, mais aussi de BMW, d’Ikea et de la banque américaine Goldman Sachs.
« La valeur est dans les batteries. Si vous perdez la valeur, vous perdez l’industrie et les emplois qui vont avec », explique Bruno Le Maire
L’autre projet est franco-allemand, lancé par les ministres de l’économie Bruno Le Maire et Peter Altmaier. « Il est indispensable pour notre indépendance technologique, pour notre indépendance stratégique, que nous réalisions nos propres batteries sur le sol européen, plaide M. Le Maire. La valeur est dans les batteries. Si vous perdez la valeur, vous perdez l’industrie et les emplois qui vont avec. »
Moins avancé que Northvolt, le projet est mieux doté : 5 milliards d’euros, dont 1,2 milliard de financement public, le tout dans le cadre des projets d’intérêt collectif de l’UE, qui permet de contourner le droit européen de la concurrence hostile aux aides publiques. Sept pays sont impliqués (Allemagne, Belgique, Finlande, France, Italie, Pologne et Suède). Deux usines sont prévues, l’une en Allemagne, l’autre en France, qui pourrait voir le jour en 2020.
Côté français, Saft, filiale de Total depuis 2016, mène le bal des vingt entreprises à ce jour impliquées (dont Solvay, Manz, Umicore, Siemens). PSA a déclaré publiquement son intérêt pour le projet mais n’a pas encore formellement signé. Bruno Le Maire, qui s’implique fortement sur ce dossier, a bon espoir de poser la première pierre de l’usine pilote française avant la fin de cette année.
Obstacles financiers et hésitations technologiques
Globalement, tout le monde est donc d’accord : il faut y aller. Et vite. Dans le détail, c’est un peu moins évident. Le problème majeur réside dans le montant faramineux des investissements. Les estimations de la mise de fonds pour produire annuellement 10 GWh de stockage varient entre 2 milliards et 4 milliards d’euros.
« La production de cellules de batteries, c’est une industrie extrêmement intensive en capital, confirme Christophe Gurtner, ancien de Saft, fondateur et PDG de Forsee Power, entreprise française spécialiste des batteries pour bus et scooters, qui a choisi la sélection et la qualification des cellules plutôt que leur production. Le travail chimique est long et coûteux : de dix à quinze ans de recherche pour mettre au point la bonne cellule à partir des bons matériaux. Cela ressemble à l’industrie du microprocesseur, avec des process très pointus et une mise de départ très importante. »
« Aucun industriel n’ira s’il n’y a pas des aides massives de l’Union européenne », avertit Yann Vincent, de PSA. « Les gouvernants font beaucoup d’annonces, mais leur agenda n’est pas forcément le même que celui des industriels, s’agace un acteur du projet. Les concurrents asiatiques n’ont pas les mêmes obligations environnementales et sociales que les entreprises européennes. Clairement, il va falloir faciliter l’accès aux financements de l’Union pour les sociétés de l’Union. »
Un défi technologique, chimique, mais aussi géopolitique
Il faut ajouter à ces réticences les divergences potentielles sur la stratégie technologique à adopter. Pour de nombreux observateurs, en particulier en Allemagne, il est absurde de courir après les Coréens et les Chinois, qui ont plus de dix ans d’avance, il faut passer directement à la génération de batteries suivante. Chez Saft, on travaille d’ailleurs davantage sur la batterie dite « tout-solide », plus compacte, plus sûre et moins polluante, que sur la lithium-ion à électrolyte liquide actuelle.
C’est finalement une impression d’avancée volontaire mais en ordre dispersé qui domine. C’est particulièrement perceptible en Allemagne. D’un côté, le patron de Volkswagen (VW), Herbert Diess, appuie fortement l’idée que l’Europe doit fabriquer elle-même ses cellules de batteries, en phase avec son ministre de l’économie, Peter Altmaier, la plupart des organisations patronales et le syndicat IG Metall.
De l’autre, Bosch, premier sous-traitant automobile mondial, a décidé début 2018 de ne pas investir dans une usine de fabrication de cellules de batteries. Un choix souvent approuvé au sein du Mittelstand allemand – ces industries de taille moyenne très présentes dans la chaîne de sous-traitance automobile. « La décision de Bosch est juste, assurait mi-2018 au Monde le patron d’une grosse PME allemande spécialisée dans les pièces de précision pour moteur à explosion. Nous avons déjà fait l’erreur, en Allemagne, de croire que nous pouvions produire nous-mêmes des panneaux solaires. Les Chinois, les Coréens et les Japonais nous ont battus à plate couture. »
L’hésitation est de mise chez les constructeurs
Chez les constructeurs, l’hésitation est aussi de mise. Renault, pionnier français de l’électrique, qui a son propre système d’approvisionnement électrique lié à son partenaire Nissan, se fait tirer l’oreille pour rejoindre l’ « Airbus » franco-allemand des batteries. BMW a plusieurs fers au feu, participant, d’un côté, au projet Northvolt, mais faisant venir à Erfurt, en Allemagne, le chinois CATL dans un projet d’usine deux fois supérieur à la gigafactory de Tesla.
Alors, que faire ? « Oui, il faut mettre en place une solide filière européenne de la batterie, résume David Labrosse, chef du planning produits au centre européen de recherche de Hyundai-Kia à Francfort. Mais c’est un immense défi. Un défi technologique, chimique mais aussi géopolitique. »La question de l’approvisionnement en matières premières sera aussi cruciale. L’usine Northvolt est construite dans le nord de la Suède pour se rapprocher des sites miniers. Comme la pétrochimie s’était installée près des puits de pétrole au début du XXe siècle.
> Lire l'article sur le site du Monde
Média
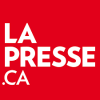
Partager